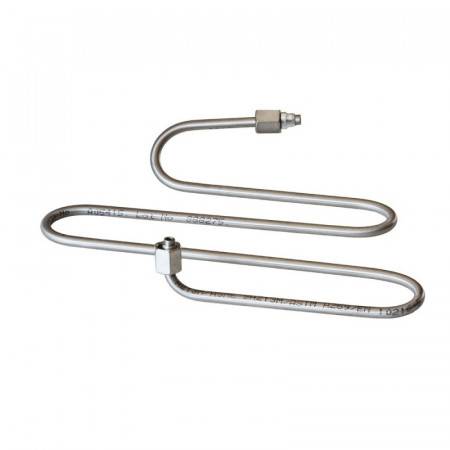
Compressor COLTRI MCH22/MCH30/MCH36/MCH45 and Open 400V Three Phase
Compressor COLTRI MCH22/MCH30/MCH36/MCH45 and Open 400V Three-Phase
The MCH22/30/36/45 OPEN range has been designed to meet the following requirements: an uncompromising compressor for intensive use, hot environments (poorly ventilated rooms or tropical countries), oversized cooling and control systems for efficient monitoring of compressor operation. Equipped with 2 flexible inflation outlets at the front, inter-stage pressure and oil pressure gauges, oil level and ventilation air temperature safety device, direction of rotation detector, drive motor, robust compressor block with oil pump and oil filter, automatic bleed valves and an electrical cabinet managing the automatic shutdown of the compressor.
The MCH30/36 OPEN range is equipped with the MCH36-V5 compressor block developed by COLTRI since 2005 and constantly improved to meet the performance, air quality and robustness requirements required for use in the most severe conditions.
A proven compressor block!
The MCH36-V5 block is built to last. It has been tested under the most extreme conditions thousands of times around the world.
Adopted by the managers of the largest diving centers in Europe, Egypt, the West Indies, Polynesia and Asia for its reliability and ease of maintenance.
With more than 10,000 machines in operation in fire and rescue services in Europe, North America and Asia, it is capable of providing high load rates at operating pressures ranging from 330 bar up to 420 bar.
The MCH36-V5 blocks are also embarked on military vessels to meet the needs of onboard security services and divers.
Proven in the steel, automotive, plastics and petrochemical industries to meet production needs under severe conditions of use, it can also be used to meet the needs of specific industrial processes.
It is in service in the security services of many airports and is also used by fire safety groups and military training academies. It is the compressor adapted to diving centers welcoming more than 50 divers / day.
Quality of the compression block
The MCH36-V5 compression block is designed for professional applications. This is the essential component of the machine on which COLTRI has left nothing to chance.
All materials are machined in high energy performance light alloys for increased reliability.
The ground cylinders have undergone an ionic nitriding treatment, which results in a high surface hardness that provides high resistance to wear, friction, abrasion and seizure.
The crankshaft is mounted on robust SKF bearings that guarantee a long service life even at high temperatures.
The low pressure gear oil pump and oil filter allow operation under severe operating temperature conditions.
The block is painted with a special paint that allows excellent heat dissipation while ensuring its protection against external aggressions in saline atmospheres. The paint makes maintenance easier when cleaning the cooling coils.
The 316L stainless steel inter-stage cooling coils are oversized in length (2 meters more on average on each stage) and in diameter to ensure optimal cooling and to allow for increased autonomy of the filtration cartridges.
Separators on the 2nd, 3rd and 4th stages remove a maximum of moisture before entering the final filtration system.
The COLTRI MCH36-V5 block is designed to compress mixtures of air and NITROX up to 40% Oxygen.
A solid frame!
The mechanically welded chassis of the OPEN range integrates the electrical cabinet, the pressure gauges on the 4 stages, the oil pressure gauge, the oil level safety device, the ventilation air temperature safety device, the direction of rotation detector, the electric motor, the compressor block, the automatic bleeding and automatic stop system and the filtration system. Powder coated epoxy resin paint provides effective protection in hostile environments.
A simple and reliable control system!
In order to optimise the reliability of the machine in all environments (heat, humidity, saline environments, storms, cold, etc.) COLTRI has chosen to dispense with the control of the system by means of the standard electronic control board. The whole machine is therefore controlled by a traditional electromechanical relay system. After years of service, any faulty component can be replaced locally without delay and without constraints related to the replacement cost and parameterization of the electronic boards. However, for special industrial applications and rescue centres, a system with touch screen and pressure sensors can be optionally adapted to control every parameter and safety.
The compressor shut-off pressure switch accessible from the front allows for quick changes in the pressure range if inflation at lower pressures is required.
The pressure gauges on the 3 stages allow a precise monitoring of the machine operation.
The direction of rotation detector prevents the machine from running if, due to a problem on the electrical mains, the phases are reversed. The machine is therefore protected from the risks of reverse rotation and the cooling problems they cause.
The oil level safety and the ventilation air temperature safety ensure reliable operation of the machine even when the user is not next to the compressor.
A high-performance and environmentally friendly automatic purging system!
The automatic bleed system on the compressor is quiet and efficient. Its adjustable timer allows the purging frequency to be adapted to the ambient humidity level.
The drain block is designed to consume a minimum of air when draining condensate to maintain flow performance.
The automatic drain system is equipped with a condensate recovery system with silencers. It avoids the release of oily residues into the environment.
Filtration for Breathable Quality Air!
The compressor of the SILENT range is equipped with several filtration systems to ensure an air quality in accordance with the requirements of the EN 12021:2014 standard.
The compressor block is equipped with cyclone separators on the 2nd, 3rd and 4th stages.
The 3L HYPERFILTER final filtration (2 filter bodies of 1.5L volume) ensures filtration of oil, odours and water down to a dew point of -60°C. To minimise maintenance costs for dive centres, the cartridges can be refilled directly by the user using molecular sieve and COLTRI activated carbon vacuum packed in a factory controlled atmosphere allowing for uncompromised air quality and costs divided by 4.
As an option, it is possible to add the H.P RF500 Refrigerated Cooler to multiply the cartridge autonomy by 5. This option is ideal for industrial applications or for diving centers that require more than 1000 hours per year from their machine because the return on investment is very fast.
Technical Data Sheet:
- Height: 154.5 Cm
- Width: 80 Cm
- Depth: 102.5 Cm
- Working Pressure: 230, 300 or 330 Bars
- Energy: Three-Phase Electric
- Sound Intensity In DB(A) At 1m: 76
- Compressor Usage: Professional and Association
- Direction of Rotation Sensor: YES
- Thermostat T°C And Oil Level Sensor: YES
- Air Dryer-Cooler: OPTIONAL
- Usage Tropical or local poorly ventilated atmosphere: YES
- Nitrox 40% compatible: YES
- Automatic Drains: YES
- Automatic Stop: YES
- Rechargeable Filtration: YES
- Inter-stage pressure gauges: YES
- PRESEC-SECURED filtration: OPTIONAL
- Oil Pump And Oil Filter: YES
- Additional Separator Between 1st and 2nd Floor: YES
- Number of Flexible Outlets With Faucet: 4
- Compressor Mobility: Fixed Compressor
Equipment :
- Automatic purges and automatic shutdown
- Electrical starter cabinet with emergency stop and hour meter
- Oil level safety
- Ventilation air temperature safety device
- Pressure gauges for pressure reading on the 4 stages
- Oil pressure reading manometer
- Water and oil separator 2nd stage
- Water and oil separator 3rd stage
- Water and oil separator 4th stage
- Safety valves 1st, 2nd, 3rd and 4th stage
- Oil pump and oil filter
- Oversized, elongated cooling coils for better cooling.
- Double HYPERFILTER filtration with reconditionable cartridges
- 4 flexible outlets at the front with DIN or ETRIER inflation valve
Optional equipment :
- Refrigeration dryer RF500
- PRESEC cartridge saturation detection system
- Programmable touch screen with pressure sensors on each stage
- 1 to 4 additional outputs to pass up to 8 outputs on the front panel
COMPRESSION GROUP |
MCH 22 |
MCH 30 |
MCH 36 |
MCH 45 |
REFERENCE |
SC000040 (400V-50Hz) SC000039 (440V-60Hz) |
SC000117 (400V-50Hz) SC000118 (440V-60Hz) |
SC000309 (400V-50Hz) SC000194 (440V-60Hz) |
SC002102 (400V-50Hz) SC002104 (440V-60Hz) |
DEBIT |
450 l/min - 27 m³/h |
550 l/min - 33 m³/h |
650 l/min - 39 m³/h |
750 l/min - 45 m³/h |
ENGINE |
ÉLECTRIQUE TRIPHASÉ |
ÉLECTRIQUE TRIPHASÉ |
ÉLECTRIQUE TRIPHASÉ |
ÉLECTRIQUE TRIPHASÉ |
OPERATING PRESSURE |
232 - 330 bar / 3300 - 4700 psig |
232 - 330 bar / 3300 - 4700 psig |
232 - 330 bar / 3300 - 4700 psig |
232 - 330 bar / 3300 - 4700 psig |
POWER |
7,5 Kw (400 V - 50 Hz), (230 V / 440V - 60 Hz) |
9 Kw (400 V - 50 Hz) |
11Kw (400 V - 50 Hz) |
15Kw (400 V - 50 Hz) |
DIMENSIONS (W x H x D) |
80 x 154,5 x 102,5cm |
80 x 154,5 x 102,5cm |
80 x 154,5 x 102,5cm |
80 x 154,5 x 102,5cm |
APPROX. NET WEIGHT |
350 Kg |
360 Kg |
370 Kg |
390 Kg |
POWER LEVEL LPA ACOUSTIC |
74 dB |
76 dB |
76 dB |
78 dB |
ROTATIONAL VELOCITY |
1050 tr/min |
1250 tr/min |
1250 tr/min |
1350 tr/min |