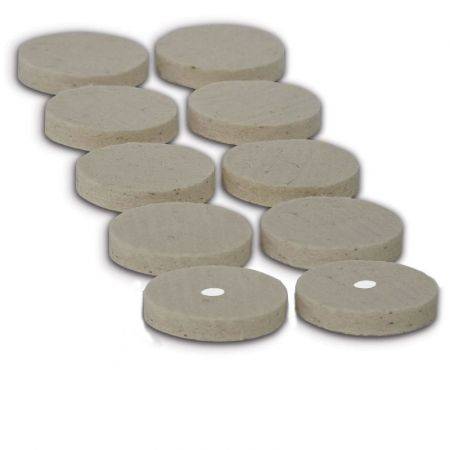
Compressor COLTRI MCH13/MCH16/MCH18 and ERGO 400V Three-phase
COLTRI MCH13, MCH16, MCH18 and ERGO Compressors
The ERGO range has been designed to meet the following requirements: focus on the essentials, a reduced budget and control systems that allow efficient monitoring of compressor operation. Equipped with 2 flexible inflation outlets at the front, inter-stage pressure gauges, oil level and ventilation air temperature safety device, direction of rotation detector, drive motor, robust compressor block, automatic bleed valves and an electrical cabinet managing the automatic stop of the compressor.
The ERGO range is equipped with the MCH16 compressor block developed by COLTRI since the end of the 1960s and constantly improved to meet the requirements of performance, air quality and robustness required for use in the most severe conditions.
A proven compressor block!
The MCH16-V18 block is built to last. It has been tested under the most extreme conditions thousands of times around the world.
Adopted by the managers of the largest diving centers in Europe, Egypt, the West Indies, Polynesia and Asia for its reliability and ease of maintenance.
With more than 90,000 machines in operation in fire and rescue services in Europe, North America and Asia, it is capable of providing high load rates at operating pressures ranging from 330 bar up to 420 bar.
The COLTRI MCH16-V18 blocks are also embarked on merchant and naval vessels to meet the needs of onboard security services and divers.
Proven in the steel, automotive, plastics and petrochemical industries to meet production needs under severe conditions of use, it can also be used to meet the needs of specific industrial processes.
In service in the military operations of many armies around the world, its robustness and reliability have made it one of the French army's selection criteria when renewing its fleet of 150 compressors dispatched to the various theatres of operation around the world.
Quality of the compression block
The MCH16-V18 compression block is designed for professional applications. This is the essential component of the machine on which COLTRI has left nothing to chance.
All materials are machined in high energy performance light alloys for increased reliability.
The ground cylinders have undergone an ionic nitriding treatment, which results in a high surface hardness that provides high resistance to wear, friction, abrasion and seizure.
The crankshaft is mounted on robust SKF bearings that guarantee a long service life even at high temperatures.
The block is painted with a special paint that allows excellent heat dissipation while ensuring its protection against external aggressions in saline atmospheres. The paint makes maintenance easier when cleaning the cooling coils.
The 316L stainless steel interstage cooling coils are dimensioned to ensure optimal cooling and allow for increased cartridge autonomy.
The COLTRI MCH16-V18 block is designed to compress mixtures of air and NITROX up to 40% Oxygen.
A compact chassis!
The welded frame of the ERGO range allows a good cooling flow and protects the user. The chassis integrates the electrical cabinet, the pressure gauges on the 3 stages, the oil level safety device, the ventilation air temperature safety device, the direction of rotation detector, the electric motor, the compressor block, the automatic bleeding and automatic stop system and the filtration system. Powder coated epoxy resin paint provides effective protection in hostile environments. Retractable carrying handles allow easy movement of the compressor for mobile applications.
A simple and reliable control system!
In order to optimise the reliability of the machine in all environments (heat, humidity, saline environments, storms, cold, etc.) COLTRI has chosen to dispense with the control of the system by means of the standard electronic control board. The whole machine is therefore controlled by a traditional electromechanical relay system. After years of service, any faulty component can be replaced locally without delay and without constraints related to the replacement cost and parameterization of the electronic boards.
The compressor shut-off pressure switch accessible from the front allows for quick changes in the pressure range if inflation at lower pressures is required.
The pressure gauges on the 3 stages allow a precise monitoring of the machine operation.
The direction of rotation sensor prevents the machine from running if, due to a problem on the electrical mains, the phases are reversed. The machine is therefore protected from the risks of reverse rotation and the cooling problems they cause.
The oil level safety and the ventilation air temperature safety ensure reliable operation of the machine even when the user is not next to the compressor.
A high-performance and environmentally friendly automatic purging system!
The automatic bleed system on the compressor is quiet and efficient. Its adjustable timer allows the purging frequency to be adapted to the ambient humidity level.
The drain block is designed to consume a minimum of air when draining condensate to maintain flow performance.
The automatic drain system is equipped with a condensate recovery system with silencers. It avoids the release of oily residues into the environment.
Filtration for Breathable Quality Air!
The compressor of the ERGO range is equipped with several filtration systems to ensure an air quality in accordance with the requirements of EN 12021:2014.
The compressor block is equipped with cyclone separators on the 2nd and 3rd stages. The MAXIFILTER final filtration ensures filtration of oil, odours and water down to a dew point of -60°C.
Technical Data Sheet:
- Height 88 Cm
- Width 92 Cm
- Depth 61 Cm
- Operating pressure 230, 300 or 330 Bar
- Energy Electric Three-phase
- Sound Intensity In DB(A) At 1m 75
- Use Compressor Professional And Associative
- Sensor Direction of Rotation Yes
- Nitrox 40% compatible Yes
- Automatic purges Yes
- Automatic shutdown Yes
- Filtration Rechargeable Yes
- Inter-stage pressure gauges Yes
- PRESEC-SECURUS Filtration No
- Number of flexible outlets with valve 2
- Compressor mobility Fixed
- Thermostat T°C And Oil Level Sensor Yes
Equipment:
- Automatic purges and automatic shutdown
- Electrical starter cabinet with emergency stop and hour meter
- Oil level safety
- Ventilation air temperature safety device
- Pressure gauges for pressure reading on the 3 stages
- Water and oil separator 2nd and 3rd stage
- Safety valves 1st, 2nd, 3rd stage
- MAXIFILTER filtration
- 2 flexible outlets at the front with DIN or ETRIER inflation valve
GROUPE DE COMPRESSION |
MCH 13 |
MCH 16 |
MCH 18 |
Reference |
SC002003 (230V-50Hz) |
SC002007 (230V-50Hz) |
SC000110E (230V-50Hz) |
DEBIT |
235 l/min - 14,1 m³/h |
315 l/min - 18,9 m³/h |
330 l/min - 19,8 m³/h |
ENGINE |
ÉLECTRIQUE TRIPHASÉ |
ÉLECTRIQUE TRIPHASÉ |
ÉLECTRIQUE TRIPHASÉ |
OPERATING PRESSURE |
232 - 330 bar / 3 300 - 4 700 psig |
232 - 330 bar / 3 300 - 4 700 psig |
232 - 330 bar / 3 300 - 4 700 psig |
POWER |
4 Kw (230/400 V - 50/60 Hz) |
5,5 Kw (230/400 V - 50/60 Hz) |
7,5 Kw (230/400 V - 50/60 Hz) |
DIMENSIONS (L x H x P) |
112 x 77 x 63 cm |
112 x 77 x 63 cm |
112 x 77 x 63 cm |
NET WEIGHT |
159 Kg |
169 Kg |
169 Kg |
ENERGY POWER LPA ACOUSTIC |
80.7 dB |
82.3 dB |
82.3 dB |